Most warehouse managers have a warehouse equipment checklist. This list should serve as a guide that outlines must-have equipment to successfully run a warehouse operation. Even for seasoned warehouse managers though, some important equipment or details may be missing from their current list.
The ideal warehouse equipment checklist should include:
- Safety equipment that meets OSHA standards
- Tools to maximize efficiency such as storage systems, warehouse management system, lift equipment, packaging materials, and conveyors
- Other items like hand tools and an equipment maintenance plan
Essential Warehouse Safety Equipment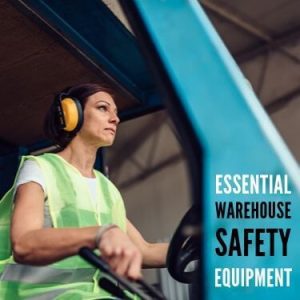
Safety first is often just an old saying used to remind us to be safe when doing potentially dangerous things. However, in 3PL warehouse operations, safety first is more than a cliche. Your warehouse equipment checklist should include the following types of safety equipment:
- First Aid Kit- The American National Standards Institute (ANSI) and International Safety Equipment Association (ISEA) developed first-aid kit requirements. Among the required items are bandages, burn treatment, and antiseptic. The full list is available online. The list outlines Class A and Class B kit requirements as well. Class A kits are for general workplaces, whereas Class B kits should be present in workplaces with additional risks involved.
- Barrier Rails- Regardless of the size or setup of your warehouse, barrier rails will be needed. These are generally used to protect equipment and structures from possible forklift damage. Barrier rails can also be used to limit employee access to high traffic forklift areas, reducing the chance of injury. Some barrier rails come with a lift out rail. The lift out rail protects valuable equipment and machines, but also provides employees access when needed.
- Hand Rails- These provide fall safety on elevated areas such as mezzanines and overhead walkways. The Occupational Safety and Health Administration (OSHA) requires that any area with a drop of four feet or more be protected. Installing a combination of hand and barrier rails is the most common solution to this requirement.
- Bollards- Known generally as a post, bollards typically serve as a visual warning to forklift drivers. Bollards can also serve the same purpose as barrier rails in protecting important machines and equipment. Multiple varieties are available in the form of permanent pour-in-place bollards and removable bollards. Sizes can also be customized based on specific needs.
- Safety Mirrors- Visibility is extremely important in a busy warehouse. Safety mirrors provide employees with the necessary visibility when moving between high-traffic areas. Depending on the physical arrangement of the warehouse, a dome or convex mirror may be better suited.
Some warehouse operators are opting for high-tech alternatives, such as motion detector sensors and sensor mirrors. Motion detector sensors can be placed in high traffic areas and alert employees of any movement in potential blind spots. Sensor mirrors combine the technology of a motion detector with a traditional mirror. They do this by showing employees the blind spots, as well as providing an audible or visual alert.
- Rack, Column, and Corner Protectors- These items all protect against potential forklift damage. Catastrophic damage and injury can occur when a forklift runs into a rack, column, or corner. Of course, drivers are thoroughly trained on how to operate a forklift, but accidents happen. Rack, column, and corner protectors can significantly decrease, and in some cases, prevent damage or injury from occurring. Safety curbs are a recommended addition as well as they protect the center section of an aisle.
- Barricade Gates- A barricade gate is essential for restricting access to specific areas. Whether an area is under construction or a safety issue is present, using a barricade gate can prevent a potential disaster. Foldable gates with wheels are a common choice due to their mobility. However, many warehouses are starting to utilize magnetic barriers. These are becoming popular due to a lower cost and the ability to have one on every aisle in a warehouse.
- Wheel Chocks- Along with first-aid kits, wheel chocks might seem obvious. However, many warehouse operations don’t utilize them. Wheel chocks are placed near a forklift’s tires when parked to prevent movement. Some wheel chocks have handles attached and also come in different materials.
- Anti-Fatigue/Anti-Slip Mats- These are a must for warehouses that have employees standing for long periods of time. It’s no secret that standing for long periods of time on a hard surface can cause aches and pains. This discomfort can lead to further health issues, as well as lower worker productivity. Anti-fatigue mats specialize in providing comfort for an extended period of time and also provide slip resistance.
- Hard Hats- In warehouse environments where an employee’s head is susceptible to injury from above, hard hats are required. This applies to any warehouse where employees operate a forklift to access items above the ground level. Class C hard hats are sufficient in most warehouses.
- Warehouse Safety Signs- Signs alone can’t prevent accidents or injuries, but in many cases they can be quite effective. Anywhere that heavy traffic occurs involving forklifts, appropriate signs need to be posted. Additional caution and safety signs need to be posted throughout the warehouse in accordance with OSHA standards as well. When purchasing signage, be sure to buy signs that specifically note OSHA compliance.
All of this equipment allow workers to use the different types of warehouse storage systems.
What are the OSHA Safety Requirements for Warehouse Equipment?
OSHA has been tasked with setting and enforcing workplace safety standards since 1970. Many of the standards set by OSHA apply to all workplaces in the U.S. However, there are some specific standards OSHA has cited more often in warehouses than others.
Warehouse operators should be aware of the following OSHA standards:
- CFR 1910.178- This standard provides guidelines for powered industrial trucks (forklifts). In 2018, OSHA documented 970 workplace injuries involving a powered industrial vehicle. 48 percent of these injuries led to a fatality. The code highlights some specific forklift rules that warehouse operators need to be mindful of:
-
- Forklifts shouldn’t be driven directly towards anyone.
- Nobody should stand or pass underneath the forks of a forklift, whether loaded or empty.
- When a forklift is unattended (the operator is more than 25 ft. away), the forks need to be fully lowered, power must be off, brakes on, and controls set to neutral.
- An authorized and posted speed limit must be followed. In areas where employees are present, a speed of 3 miles per hour is required.
- An approximate distance of three truck lengths should be maintained between vehicles.
- When approaching an intersection or any area where vision is limited, drivers need to slow down and sound their horn.
- An appropriate aisle width must be utilized. The size of the aisle will depend on the size of the forklifts and pallets being used. Narrow aisle trucks typically require a clearance of 8-10 feet, while wide aisle forklifts need 12-13 foot clearance. Forklift manufacturers include this information in their product description.
Following these and other guidelines for forklifts will lower the chances of injuries and accidents occurring. This will, in turn, reduce the possibility to receive citations and potentially large fines from OSHA.
- CFR 1910 Subpart H- Guidelines for warehouses that contain hazardous materials. Whether warehouse employees are directly or indirectly in contact with hazardous materials, there are rules that need to be followed.
For warehouses in which employees eyes or body may be directly exposed to corrosive materials, an emergency wash station is required. A Material Safety Data Sheet (MSDS) needs to be included for each separate hazardous material. The MSDS should include instructions for handling the material and spill cleanup procedure. Materials needed in case of a spill must also be readily available.
In facilities where hazardous materials aren’t directly handled, storage is the main consideration. For general flammable liquids kept inside a building, the materials must be maintained in a flammable storage metal cabinet. A portable fire extinguisher needs to be within 10 to 25 feet of the storage container. Security measures also need to be in place for the container to prevent theft or tampering.
There are additional rules and regulations in place for handling specific types of hazardous materials. These can be found online underneath subpart H of the OSHA standards.
- CFR 1910.305- Guidelines regarding electrical wiring methods. This often cited violation can be easily avoided in many cases. A licensed electrician is equipped to meet most of the guidelines when initially configuring the electrical system. However, new situations will come up after the initial setup in which rules must still be followed.
Extension cords need to be covered and protected to prevent damage to employees and equipment. Temporary wiring has to abide by this rule as well. As soon as a task requiring temporary wiring is completed, the wiring needs to be removed. If an injury or accident is caused by uncovered electrical wiring, a violation or fine is almost guaranteed to follow.
- CFR 1910.176- Guidelines for material handling and storage. This standard contains a relatively small amount of information compared to the others mentioned previously. However, the information is extremely important.
First, the standard restates the necessity of maintaining appropriate clearances in aisles. It also adds that aisles and passageways cannot be obstructed in anyway that creates an unsafe condition. Second, secure storage is mentioned and that it needs to be stored in an appropriate manner to avoid sliding or collapse.
Since the wording is a bit vague and limited in this case, it helps to know best practices. There should be at least 6 inches of clearance on the top and sides of each pallet load. Stacking should be limited and when used, place heavier loads on the bottom and lighter loads on top.
Abiding by these standards assists warehouse managers with maintaining a safe working environment and meeting OSHA compliance. Ensuring that you’re meeting OSHA compliance can be tricky. Working with R+L Global Logistics to manage your warehousing and order fulfillment can take that burden off of you.
Equipment to Improve Loading Dock Safety
Many documented warehouse injuries involve accidents that occur at or near a loading dock. Warehouse managers can ensure loading dock safety by following a few simple steps:
- Implement Fall Protection- OSHA requires docks with 4 feet or more above the lower level to have fall protection in place. Even for docks that come in under four foot, it is still recommended to have some type of fall protection. This protection can be in the form of a gate, chain, or other moveable barrier. Many warehouse operators opt for a swivel or rise gate. This option provides safety without sacrificing efficiency.
- Prevent Accidental Movement- OSHA code 1910.178 notes that during loading and unloading, vehicles need to have wheel blocks in place to prevent accidental movement. Most freight drivers have wheel chocks with them at all times. However, warehouse managers should have some on hand just in case a driver doesn’t. Accidental truck movement can cause structural damage and injury to employees.
- Structural Protection- While dock bumpers aren’t required, they are highly recommended to protect against potentially significant structural damage. Bumpers are available in a variety of sizes and materials to meet the specific needs of each loading dock.
- Effective Lighting Solutions- Dock lighting is an important feature that increases the safety of loading docks. Even if a warehouse doesn’t process freight in the dark. Simple dock lights can provide a visual aid inside trucks that aren’t equipped with lighting. Warehouses should also consider dock guide lights. This innovative product provides customizable visual cues to freight operators to ensure structural protection. An added benefit is ideal dock positioning when trucks are docking which increases loading and unloading efficiency.
- Dock Board, Plate, or Leveler- These are essential for movement and safety while loading and unloading at the dock. Load weight and transportation method will often determine which of these options is best suited for your warehouse. For lighter loads, a dock plate is typically recommended. For larger capacity loads that require the use of a forklift a dock board is often the best choice.
Dock levelers are a permanent alternative to plates and boards. Levelers are installed as an attachment to the dock itself and help bridge the gap between the dock and freight trucks.
The Right Equipment for Warehouse Security
An integral part of an overall warehouse safety program is a comprehensive security system. The complexity and scope of a security system will vary based on a warehouses’ individual needs. All systems need to address potential security factors including access control, inside & outside theft, and data security.
An effective solution to many security threats is an electronic access control system. An access control system uses key cards, fingerprints, or other individual technology to allow only certain people into the building. With this system, visitors’ access is significantly limited which increases overall security. Most systems can be customized to create secure areas within the building as well.
A motion detection and alarm system will assist with managing outside security threats. Many potential intruders can be deterred by a bright light triggered by a motion detector. However, some trespassers are more brazen and will continue their attempted break-in. An effective warehouse alarm system should notify local law enforcement and warehouse managers immediately when a security breach has occurred.
Lastly, surveillance cameras should be in place where potential theft and unauthorized entries can take place. Before deciding where to place surveillance cameras, work with your security provider to identify all potential weak spots. After cameras have been installed, managers should have access to live and past footage.
Equipment to Increase Warehouse Productivity and Efficiency
Once the safety and security of a warehouse is established, the focus should be shifted to productivity and efficiency. The productivity of a warehouse determines the overall success, while efficiency determines how well this is accomplished.
The following equipment increases warehouse productivity and efficiency:
- Storage System- Pallet racks, shelving, specialty racks
- Material Handling- Forklifts, pallet jacks, hand trucks
- Packaging- Industrial scales, stretch wrap machines, packing tables
- Conveyor- Flexible, gravity, power systems
Selecting and using the right equipment will ensure that your warehouse is always running smoothly.
Which Warehouse Storage Equipment Should I Use?
Warehouse operators have a number of options to choose from when it comes to storing products in their warehouse. A number of factors are involved when selecting the right storage system for a warehouse. These factors include available space, how orders are picked, and the size of orders.
Most warehouses have multiple storage systems to accommodate different products and picking methods. Pallet racks allow for more storage space, product consolidation, and a simpler loading and picking process. Shelving allows for storage and picking of smaller items and a wider variety of products.
Once you’ve decided to use racks, shelves, or both there are still more choices to be made. There are many different types of racks and shelves. For shelving, The majority of warehouse operators use industrial shelving. The racking system depends on the order products must enter and leave the warehouse.
A first-in, first-out (FIFO) model is for products that must leave the warehouse in the order they were received. Perishable items or items subject to expiration dates should follow the FIFO model. In a last-in, first-out (LIFO) storage model, products that arrive last leave the warehouse first. For non-perishable products, the LIFO model can generally be used which typically allows for more dense storage.
Which storage model you’ll be following will guide you to the correct storage equipment system to use in your warehouse.
Types of Warehouse Racking Systems
- Selective Pallet- This is the most common type used in warehouses. A selective rack configuration provides order pickers access to all products available without having to move other products around. Because all products have their own aisle lane, more aisles are needed leading to less storage and floor space. This is a FIFO storage option.
- Pallet Flow- If you need a FIFO system but have less product variety a flow rack might be best. This system uses gravity to move pallets from the loading end of an aisle to the picking zone. Specialized rollers and brakes are needed to control movement which ensures safety when pallets are rolling. Flow racks can store pallets from two to twelve deep, greatly increasing the storage capacity of products.
- Drive-Through Rack- This rack setup is used for FIFO storage and also offers high-density storage. Pallets are loaded through one end of the system and unloaded through the opposite end. Busy warehouses use this system as it allows loaders and unloaders to work simultaneously without interrupting one another.
- Double Deep- In a double deep racking system, pallets are stored back to back in the same aisle lane. This creates a LIFO storage model as the last products in are the first to go out. Each product has its’ own aisle lane. While this setup leads to more storage and floor space, it often comes with increased costs. Special forklifts such as a reach truck or fork attachments are needed to load and unload the double deep pallets.
- Drive-in Rack- Similar to a drive-through rack, forklifts drive into an aisle lane to load and unload pallets. However, this system uses the same aisle for entry and exit and follows a LIFO storage model. Warehouses with less product variety and a desire for more pallet storage may want to use this model.
- Push-Back Rack- This FIFO storage rack option uses limited aisles and provides exceptional product storage. Similar to a drive-in rack, this configuration allows for storage of multiple deep pallets of the same product. However, the driver doesn’t need to drive into the aisle lane to load or unload the product. When pallets are loaded and unloaded, they are pushed back and forward.
- Specialty Racks- If you store products that aren’t palletized or boxed, you’ll likely need specialty racks. There are a variety of specialty racks depending on the type of equipment you have:
- Cantilever rack- Store long items like lumber, pipes, or metal beams
- Reel & spool rack- Store chain, hose, cable rope, wire and more
- Drum & barrel racks- Store drums and barrels full of non-hazardous liquids
Choosing the right storage system for a warehouse can be challenging. It can be frustrating to select a storage system and realize that it’s not as efficient as you anticipated. Luckily, R+L Global Logistics operates a number of fulfillment warehouses. Using our services eliminates the headache of having to deal with making these time-consuming decisions.
Importance of a Warehouse Management System
Managing all of the processes involved in a warehouse operation can be extremely difficult. To simplify this task, most warehouses utilize a warehouse management system (WMS). This system organizes all aspects of warehouse fulfillment including inventory tracking, picking & packing, shipping, receiving, and more. A WMS can be integrated into an enterprise resource planning system (ERP), which links together additional business aspects.
A warehouse management system is essential to efficient warehouse operations. Bringing together all of the necessary pieces of warehouse processes into one system creates organization and improves accuracy.
Material Handling Equipment Needed in a Warehouse
Moving products from one area to the next in a warehouse takes up a significant amount of time. Having an efficient process to transport and handle materials can greatly increase warehouse productivity. An important part of this process is making sure that the right equipment is available in your warehouse.
Warehouses should have the following material handling equipment on-hand: Forklifts, pallet jacks, hand trucks, and platform trucks. All equipment should consider the size and maximum load capacities of the products that will be handled.
When choosing which forklift(s) to use in your warehouse, pallet location and rack system should also be taken into account. Each racking system has a recommended forklift type that should be used. Counterbalance forklifts are the most common forklifts used in warehouse operations. However, even just for counterbalanced forklifts, there is a wide selection available based on specific warehouse needs.
Choosing the Right Warehouse Packaging Equipment
If you’re a warehouse manager looking to improve your packing process, equipment should be a top priority. Giving your employees the necessary tools for packing will increase efficiency and productivity.
Warehouse operators should include these pieces of packaging equipment as part of their overall checklist:
- Industrial Scale- This valuable tool will provide accurate measurements when preparing products for shipment. If you’re shipping products on pallets, this scale is a must. Scales come in a variety of weight capacities which typically affect the cost.
- Edge and Corner Protectors- When shipping tightly-packed products, edge and corner protectors are essential for product safety. These can also be used to protect when using metal strapping.
- Strapping Tools- Whether you’re bundling multiple products or reinforcing a package, strapping serves a valuable purpose. If cost isn’t a major factor and order count is high enough, an automatic strapping machine is worth the investment. Otherwise, you will need a tensioner, sealer, cutter, and seals to manually strap outgoing loads.
- Stretch Wrap Machine- This is a highly efficient tool when shipping a large quantity of palletized products. A stretch wrap machine is able to fully wrap a pallet in a fraction of the time that an employee can. There is a steep cost involved, but this cost can be recovered in the long run when productivity is significantly increased.
- Packing and Lift Tables- If you have employees manually packing products to be shipped, they’ll need a workspace. A simple packing table can certainly suffice, but warehouse managers should consider a lift table. Instead of employees manually moving products between the floor and a table, a lift table does the work. This reduces the amount of stress on employee’s backs and improves overall ergonomics.
This equipment is in addition to the basics like boxes, bubble wrap, shipping peanuts, labels, and more.
Do I Need a Conveyor System in my Warehouse?
Conveyor systems can have a significant impact on efficiency and productivity in warehouses operations. However, these systems often come with a high cost, from the initial purchase to installation to cost to operate and maintenance.
Conveyor systems are needed in a warehouse if productivity and efficiency can be significantly improved. Employees may be spending too much time moving products in the warehouse. Warehouses not meeting productivity goals should consider adding a conveyor system or adjusting an existing one.
If you’ve decided to implement a conveyor system in your warehouse, you’ll have a number of choices available. Power, gravity, and flexible are just three common types of conveyor systems used in warehouses. The system that you ultimately use will depend on a number of factors including cost, physical layout, and automation tools.
Miscellaneous Warehouse Equipment
All of the equipment that’s already been mentioned up to this point is vitally important to warehouse operations. However, there is some additional equipment that many warehouses use on a daily basis.
Warehouse managers should consider including:
- Mezzanines- This raised platform adds space to your warehouse without expanding your facility.
- Warehouse Offices- A blocked-off office can provide the necessary privacy and noise reduction needed for some tasks or employees.
- Rolling Ladders- For non-palletized products on high shelves, this provides on-the-go convenience for employees.
- Warehouse Gloves- Although not required in most warehouse environments, gloves increase safety and comfort for employees that regularly handle equipment.
- Fans and Heaters- Provide air and heat in warehouses that don’t have central systems.
Equipment Maintenance Plan
No matter what kind of equipment you have in your warehouse, a maintenance plan needs to be present and documented. Most equipment manufacturers provide information for recommended maintenance when purchasing the equipment. Some manufacturers include and offer maintenance through their own company.
All employees that operate any equipment with a maintenance plan should be familiar and know where the plan is. Forklifts specifically are required by OSHA to have a daily inspection which should be included in a maintenance plan. Although this doesn’t need to be documented, it should in case of an accident or OSHA investigation.
R+L Global Logistics' Warehousing Expertise
The information and tips provided in this article will help you successfully launch and run a fulfillment warehouse, from following the warehouse equipment checklist to offering fulfillment solutions. However, setting up and operating your warehouse can take a significant amount of time and energy.
This is why many businesses choose to work with R+L Global Logistics. Working with our team will free up your time to allow you to focus on more key aspects of your business, whether you are storing batteries or other merchandise or deciding between warehouse vs distribution center options. You can trust that our industry-leading resources and expertise will have your business operating at peak productivity and efficiency.
Contact us to find out more about how we can help your business thrive and grow.
I'm glad you elaborated on warehouse storage models and how the one we select for our business helps us understand what kind of equipment we'll need. My cousin and uncle are interested in starting a warehouse business in a few months, so I'm sure they'd benefit from reading your insight on storing special products and what kind of racks and equipment you'll need for them.
PLEASE KINDLY REQUEST IF CAN SEND ME DETAILS OF ALL WAREHOUSE OPERATIONAL INFORMATION